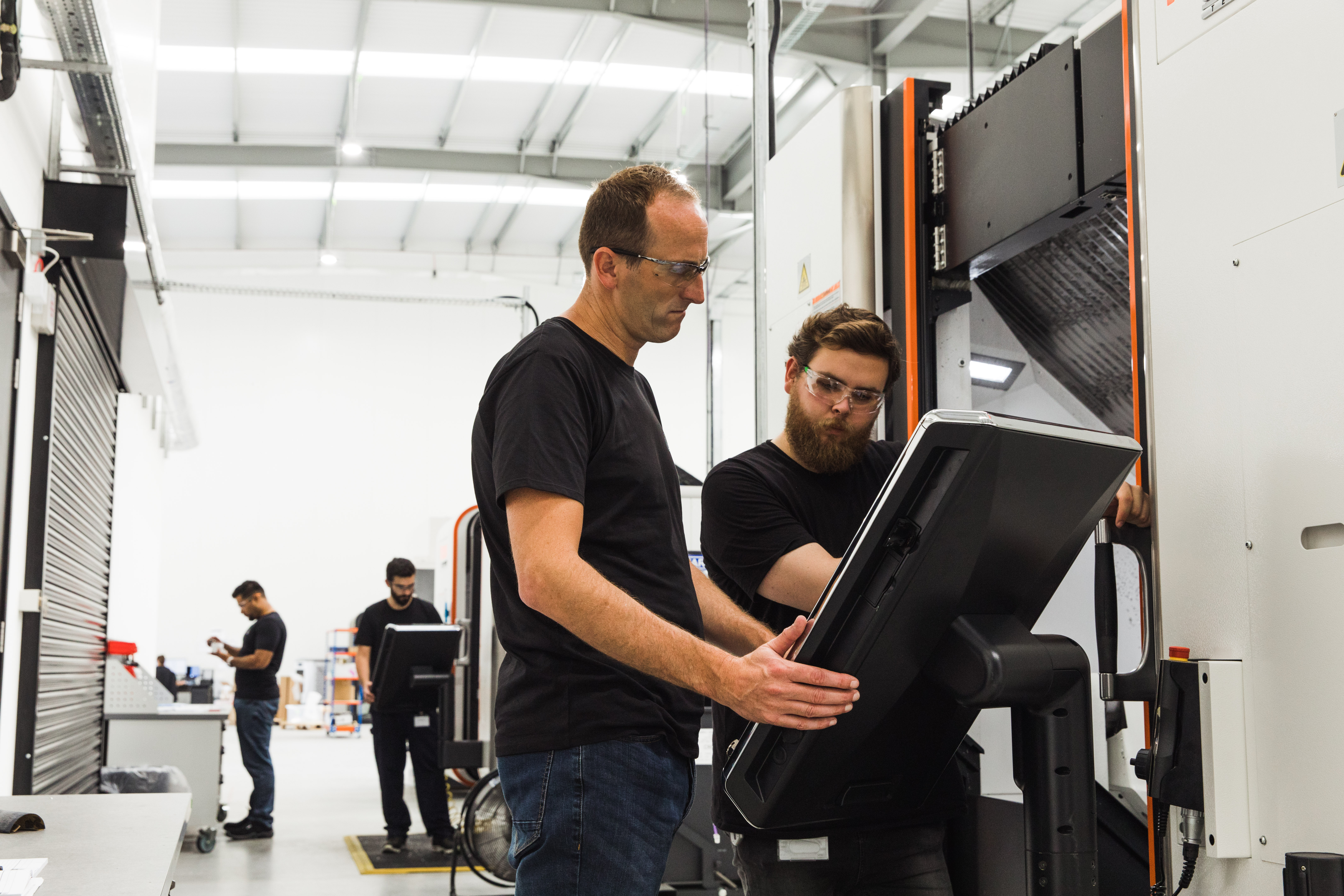
If you have typed “how to increase cnc capacity without new machines” into a search engine, you already know that buying another machining centre is not the only – or the fastest – way to ship more parts. Many job shops still run at only 60 – 65 percent spindle utilisation even when the order book feels full. The cheapest machine you can invest in is therefore the one you already own.
Below is a practical roadmap, tested in CloudNC’s own facility and across hundreds of customer sites, for unlocking extra capacity without adding a single new machine tool. These strategies will help you increase CNC capacity without new machines in days, not months.
1. Measure and expose hidden downtime
You cannot improve what you cannot see. Start with automatic machine‑monitoring software to log every minute of spindle status. Within a week the real causes of lost hours will emerge – tool probing errors, manual program edits, or operators waiting on CMM sign‑off.
Share simple utilisation dashboards at the daily production meeting. When machinists see that yesterday’s flagship 5‑axis mill cut metal for only 4.2 of its 10 scheduled hours, the hunt for root causes begins naturally. This awareness alone can increase CNC capacity without new machines by reclaiming idle hours you already pay for.
2. Cut setup time with standardisation and quick‑change
Setup is the black hole that swallows machine hours. A peer‑reviewed SMED case study on a turning line reported more than 45 percent reduction in setup time once internal tasks were optimised and quick‑change fixtures installed. Use that freed time to run smaller lots more often – effectively adding productive hours to every shift.
Key levers:
1. Process Sheets with Photos
Visual, step-by-step guides eliminate reliance on tribal knowledge and prevent wasted time searching for torque specs, gauge lengths, or setup info. They also make onboarding new machinists faster and easier, enabling them to follow standard procedures confidently from day one.
2. Modular Fixturing & Zero-Point Clamping
Swap fixtures or vices in minutes using standardized base plates and zero-point systems. This greatly reduces setup time, and often pays for itself within the first few jobs.
3. Standardised, Pre-Set Tooling
Maintain a core set of tools permanently loaded and pre-set in the machine. This eliminates building and setting tools for repeat jobs, streamlines programming, and ensures consistency across setups.
4. Well-Defined Tool Database
Centralise tooling data in a digital library with predefined cutting parameters (feeds, speeds, depths and widths of cut) for every material your shop cuts. Ensures consistency, reduces programming time, and supports CAM automation.
5. Standardised Datums
Apply a universal coordinate system across fixtures and machines. This simplifies CAM programming, enables seamless fixture swapping, and supports fast, repeatable setups.
6. In-Cycle Probing
Automate offset setting, part alignment checks, and tool breakage detection mid-cycle. Boosts reliability and enables unattended or lights-out machining.
3. Unlock lights‑out machining
Your spindle does not need coffee breaks. Even modest unattended running can transform output. One Ventura, California shop added two seven‑axis robots and gained 64 unattended machining hours per week).
Getting started:
- Begin with aluminium or plastic parts featuring relaxed tolerances, capable of accommodating minor variations during unattended operation.
- Use bar feeders, pallet pools, or robot loaders with tombstone or modular fixturing to enable continuous operation, reducing changeovers.
- Maximise spindle time by machining several parts from one billet, reducing manual reloads and increasing unattended runtime.
- Use spindle load macros, tool break detection, and in-machine probing to identify failures before they cause scrap. Add webcams or IP cameras for visual checks.
- Carry out in-process inspection first thing in the morning to confirm parts remain within tolerance and catch any issues before full lights-out batches are completed.
- Start with short evening runs (2–4 hours) and scale up to overnight as reliability grows.
4. Program faster and cut smarter with CAM Assist
Programming often dictates machine idle time. CAM Assist – CloudNC’s AI plugin for CAM toolpath generation – automatically generates complete machining strategies in minutes and has delivered up to 80 percent reductions in programming time for users. Faster programs reach the machine sooner, freeing CAM engineers to queue more jobs.
Early deployments of its physics‑based Cutting Parameters engine also show productivity gains of at least 20 percent (often realised as cycle‑time savings) in real shops.
5. Sequence jobs for flow, not ticket order
Running parts strictly in quoted order feels fair but traps capacity. Instead:
- Group by material and tooling to avoid unnecessary swaps.
- Back‑fill small prototype jobs during CMM or deburr waits on larger batches.
- Reserve the most automated machine for overnight work every day, even if it means reallocating jobs.
Thoughtful scheduling alone can add multiple productive hours per shift and increase CNC capacity without new machines immediately.
6. Maintain before failures steal shifts
Unexpected breakdowns destroy capacity goals. Deloitte research shows that poor maintenance strategies can slash a plant’s productive capacity by 5–20 percent (source: l). A simple preventive‑maintenance routine – daily lubrication checks, weekly spindle‑load reviews, quarterly laser calibration – costs little but protects uptime.
To avoid downtime to unexpected breakdowns:
- Implement a preventive maintenance schedule with periodic tasks.
- Do daily checks on lubrication, coolant levels, and machine cleanliness.
- Perform quarterly calibrations like laser alignment and backlash checks.
- Keep clear maintenance logs for tracking issues and fixes.
- Train operators to spot and report early signs of trouble.
7. Build a culture of continuous improvement
Kaizen boards, 5S audits and small‑group problem‑solving sessions carve minutes from every process. Celebrate each improvement by posting the regained spindle hours on the shop‑floor screen. Momentum multiplies.
Frequently asked questions
Q: How can I increase CNC machine capacity without buying new equipment?
A: Boost CNC capacity with smarter scheduling - group parts by material and required tooling, run jobs back-to-back, and extend into evenings. Standardise setups using existing equipment to reduce changeovers and downtime.
Q: What is a good spindle utilisation rate for a job shop?
A: Top performers exceed 80 percent, while the industry median is 60 – 65 percent .
Q: Is robot automation worth it for small batch sizes?
A: Even a low‑cost pallet pool or cobot can add 40 + unattended hours each week, paying back in 12‑18 months.
Next steps
If you are ready to increase CNC capacity without new machines, get started with CloudNC. We will show how CAM Assist can unlock hidden hours across your existing fleet.
Stop waiting for capital budgets – start making the most of the machines you already own today.